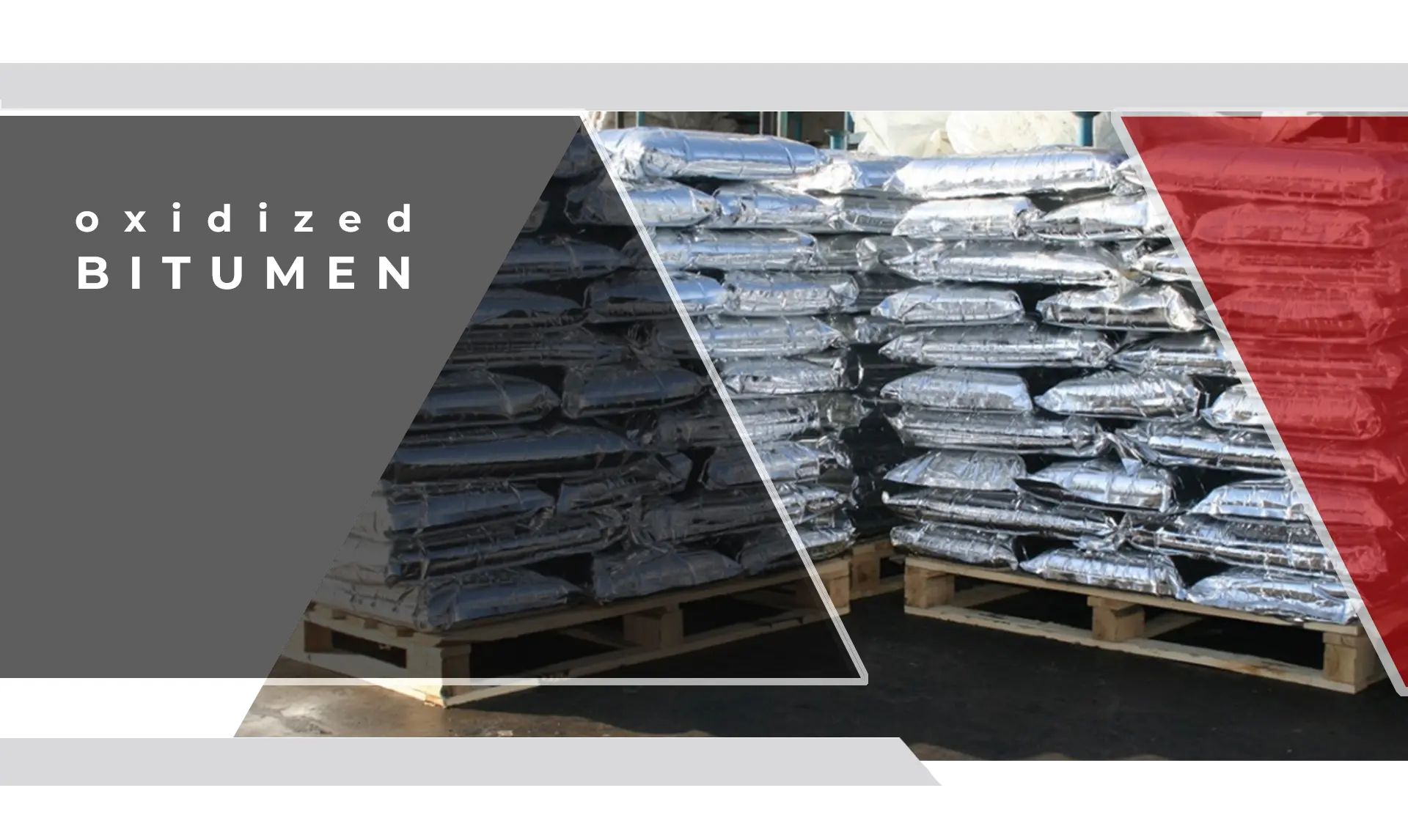
Oxidized Bitumen
What is Oxidized Bitumen?
Oxidized bitumen, also known as blown bitumen, is a specialized form of bitumen created through a process of air blowing. This variant, characterized by low penetration and a high softening point, is utilized in various manufacturing processes and as a sealing agent. Compared to pure bitumen, oxidized bitumen exhibits lower penetration, indicating it is softer and less susceptible to temperature fluctuations.
The designation for oxidized bitumen is “R,” denoting its softening and penetration characteristics. For instance, R80/25 bitumen has a softening point of 80 degrees Celsius and a penetration value of 25.
How is Oxidized Bitumen Produced?
Oxidized bitumen is manufactured by blowing air through petroleum bitumen, a process that enhances its softness and elasticity, particularly in cooler conditions. During the final purification stage, hot air is injected into pure bitumen, resulting in a rubber-like grade of bitumen.
This procedure involves passing hot air, typically between 200 to 300 degrees Celsius, into a chamber filled with bitumen via perforated pipes.
The interaction of hot air and bitumen leads to a chemical reaction where hydrogen atoms from the bitumen’s hydrocarbon molecules combine with oxygen, forming water and initiating a sintering process that yields oxidized bitumen.
Applications of Oxidized or Blown Bitumen:
Oxidized bitumen is utilized in the oil and gas industries for coating materials on pipelines and their joints. It also finds use in the electrical industry as a sealant for wire coatings. In the construction sector, blown bitumen is integral to waterproofing applications, such as producing roofing felt sheets for factories.
Additionally, oxidized bitumen is employed in bitumen and asphalt plants for road surfacing and serves as a key component in sound-dampening layers for acoustic insulation.
In essence, oxidized (blown) bitumen is primarily used in industrial applications, including waterproofing for roofs and floors, tire manufacturing, pipe coating, and paint formulation.
Properties of Oxidized Bitumen:
Oxidized bitumen is classified based on its softening point and penetration degree. For example, 85/40 bitumen has a softening point of 85±5 °C and a penetration degree of 40±5 dmm.
These types of bitumen adhere to standards concerning solubility and heat-related weight loss. Oxidized bitumen has a significantly higher softening point than corresponding penetration bitumen, resulting in greater thermal sensitivity. For instance, their penetration index is considerably higher, ranging from +2 to +8.
Types of Oxidized Bitumen:
There are various grades of oxidized bitumen, each suited to specific applications.
Some common grades include:
- Oxidized bitumen R75/30
- Oxidized bitumen R95/25
- Oxidized bitumen R85/25
- Oxidized bitumen R90/40
- Oxidized bitumen R105/35
- Oxidized bitumen R115/15
These grades are widely used in industrial applications such as waterproofing, tire production, pipe coating, and paint manufacturing.
For instance, oxidized bitumen 75/30 is produced by polymerizing flexible bitumen in response to air exposure. With a penetration grade of 30 and a softening point of 75, this grade is employed across various industries, including road construction, hydropower projects, roofing, and electrical applications.
Oxidized bitumen 95/25 is a standard grade used in construction for purposes such as steel pipe covering and waterproofing. It is derived from blowing hot air through penetrating bitumen to achieve the desired specifications.
Availability and Ordering:
Grand Petroleum Company provides Penetration Grade Bitumen at competitive prices, available in both drum and bulk formats for local and global markets. To inquire about the latest pricing or to initiate an order, Contact Grand Petroleum Sales Department.
Oxidized Bitumen R85/25
Oxidized bitumen 85/25 is the most widely used type of bitumen in the construction industry, and the main grade of this type of bitumen is 85/25 bitumen.
Oxidized bitumen 85/25 has a softening point of 85 and its penetration degree is 25. Among the types of oxidized bitumen, this bitumen is widely used and very popular in the market for paving, road maintenance, embankments, dams in water projects, the roofing industry, flooring, tile of bathrooms, coating pipelines, lithium battery, glue for laminate boards, etc.
Oxidized Bitumen R85/40
Oxidized bitumen 85/40 is based on petroleum bitumen made by blowing 60/70 bitumen with very hot air.
Oxide bitumen 85/40 is used in making waterproofing layers, asphalt clays, sealing roofs, mastics, pipe coating, paint, even road asphalt, and many other things.
Oxidized Bitumen R105/35
Oxidized bitumen R 105/35, which is the result of the oxidation of penetrating bitumen exposed to very hot air, is completely hard at ambient temperature and requires a lot of heating to use it.
Oxidized bitumen 105/35 is used in civil engineering, construction, road operations, crack sealing, road repairing, roofing, flooring, coating, protecting pipelines, insulation, and sealing buildings.
Also, R105/35 is used in petroleum operations for coating oil and gas pipelines as a carriage sealant and soundproofing material in cars, in very hot or very cold weather conditions.
Oxidized bitumen 105/35’s in combination with gilsonite can maintain asphalt stability. Also, its combination as we said with gilsonite can prevent deformation and crack due to changing climates.
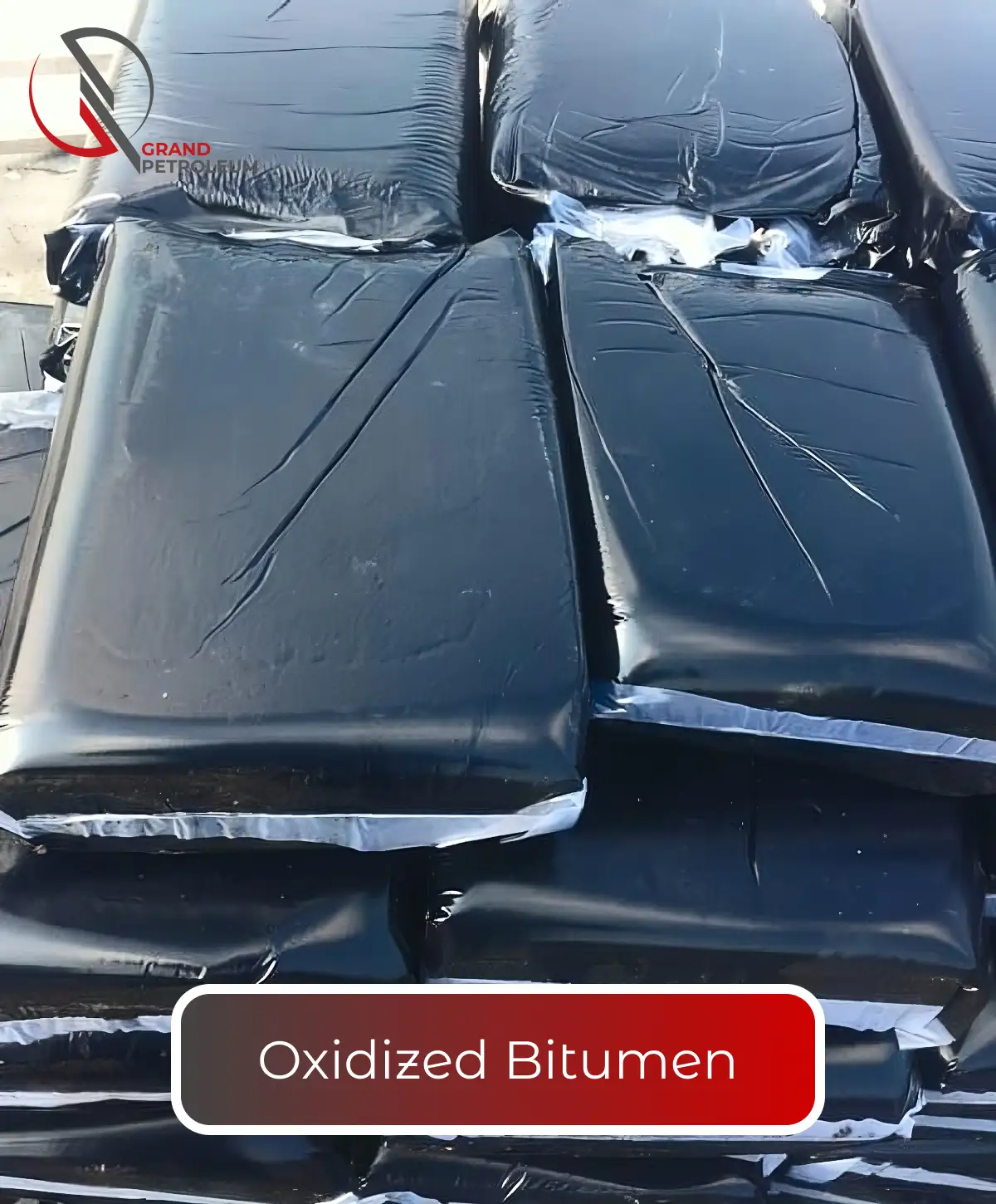
Oxidized Bitumen R115/15
Oxidized bitumen 115/15 is obtained from the reaction of hot bitumen with oxygen. Bitumen aeration is a process in which hot liquid bitumen is exposed to air.
Blown bitumen 115/15 is used in making waterproofing layers, asphalt clays, sealing roofs, mastics, pipe coating, paint, even road asphalt, and many other things.
Production Process of R115/15
The manufacturing of oxidized bitumen R115/15 follows a precise and carefully monitored process:
- Heating :
Bitumen is heated to high temperatures (around 240–300 °C) to transform it into a molten state.
- Aeration :
Air is blown through the molten bitumen under controlled conditions, triggering a chemical reaction that increases its viscosity and thermal resistance.
Cooling and Grading :
The oxidized bitumen is cooled and graded based on its softening point (115 °C) and penetration value (15 dmm).
Properties of Oxidized Bitumen R115/15
•High Softening Point: Ensures resistance to deformation under high temperatures.
•Low Penetration Value: Provides excellent hardness and durability.
•Waterproofing Capability: Perfect for creating impermeable layers.
•Thermal Stability: Performs consistently in extreme weather conditions.
•Chemical Resistance: Resists degradation from chemicals, acids, and alkalis.
Index | Standard | Oxidized Bitumen Grade | |||||
75/30 | 85/25 | 85/40 | 95/25 | 105/35 | 115/15 | ||
Softening Point Temperature © | ASTM D36 | 75±5 | 85±5 | 85±5 | 95±5 | 105+5 | 115±5 |
Penetration at 25 C (dmm) | ASTM D5 | 30+5 | 25±5 | 40+5 | 25±5 | 35+5 | 15±5 |
Thermal Loss Percentage | ASTM D1754 | 0.2 | 0.2 | 0.2 | 0.2 | 0.2 | 0.2 |
Solubility in trichloroethylene | ASTM D2042 | 99.5 | 99.5 | 99.5 | 99.5 | 99.5 | 99.5 |
Manufacture of Oxidized Bitumen
The production of oxidized bitumen involves several steps:
1. Feedstock Selection: It starts with the choice of quality crude oil feedstock and the accurate chemical composition to be employed.
2. Distillation: The oil is distilled into the naphtha, in which the bitumen fraction is separated.
3. Oxidation: The tar portion is next heated, and air is forced through it, causing the oxidation process to begin. This step can be carried out using different methods, such as:
- Air Blowing: The heated air is passed through molten bitumen, and this oxidation process forms byproducts.
- Catalytic Oxidation: The catalysis process is achieved by the inclusion of accelerators, which enable lower temperatures and shorter timeframes for the processing.
4. Cooling and Packaging: Ultimately, the oxidized bitumen is cooled and packed for shipment once the targeted oxidation level is attained.
The process of production is meticulously managed to guarantee uniformity in quality and fulfil the performance specifications applicable to different fields of application.
The applications and uses of oxidized bitumen
Oxidized bitumen is widely used across various industries due to its unique properties and versatility:
Roofing Membranes and Waterproofing: From the point of view of the commercial application of oxidized bitumen, we could mention roofing membranes and waterproofing systems with high performance and long service life. Among the positive qualities of this material are its great durability, resistance to ageing weathering, as well as to high temperatures. Therefore, it is best to protect the external part of the buildings and structures from extreme weather conditions.
Pipe Coatings and Linings: Oxidized bitumen is favoured as the prime coating material for pipes and is in line with pipes which are used in the oil and gas industry. Due to the chemical properties and scratch factor of the pipelines, the chances of corrosion and destruction are minimized; thus, their lifetime is extended greatly.
Pavement Construction: bitumen is created from oxides, which are applied to asphalt paving and resurfacing. Although it is primarily a pavement quality and life enhancer and aids in preventing rutting, cracking and ageing.
Industrial Applications: Degraded bunker bitumen, after being oxidized, can further venture into the oil market and, apart from these, concentrate on the following:
Sealants and adhesives
Metals and concrete
Electrical insulation materials
Sound absorbents and vibration dampers are the materials.
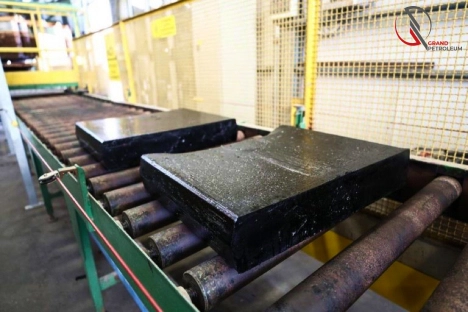
Reasons for Employing Oxidized Bitumen
Oxidized bitumen offers several advantages over conventional bitumen:
High-Temperature Resistance: Asphalt is probably the biggest beneficiary of its ability to withstand the high softening point and thermal stability, which makes it possible to withstand even high temperatures, for example, those which come during the production of a road and roof.
Weathering and Aging Resistance: Oxidation makes the material fit for antiquing, and this way, the structure moves from decaying and weathering but can instead highly last for long at the best quality that it can be.
Flexibility and Durability: The oxidation of bitumen is the main cause of ageing, and the wider temperature range has an effect on the bitumen, allowing it to resist cracking and brittleness and have good durability.
Cost-Effectiveness: Since the use of oxidized bitumen is more complicated than traditional bitumen, it remains a cost-effective solution with the advantages of minimal maintenance needs and stronger durability over time.
Exploring the Production Process in Depth
There would be no point in saying the word bitumen without, first of all, learning how it is produced. I believe our next mission should consist of researching the production process. The conduction of the oxidation step features a very large part of the reacting process that consequently modifies the end product.
Air Blowing Method
Exposure to the air is one of the most popular oxidizing agents. Hot air is constantly being blown through during the heat seal operation of bitumen through hot air, which is generally between 240 ºC and 300 ºC (464 ºF and 572 ºF). The airflow and temperature are monitored very strictly in order to keep up with the necessary level of oxidation.
The chemical process then starts when the hot air adheres to the bitumen and triggers a very complex series of chemical reactions. These species, through their interaction, reorganize the structure and cross-link existing molecules as well as the oxygen atoms with bitumen’s simpler molecule groups.
It may take several hours, depending on the characteristics of the final product. However, it should be clear that the oxidation process proceeds further as the point of melting and viscosity increase.
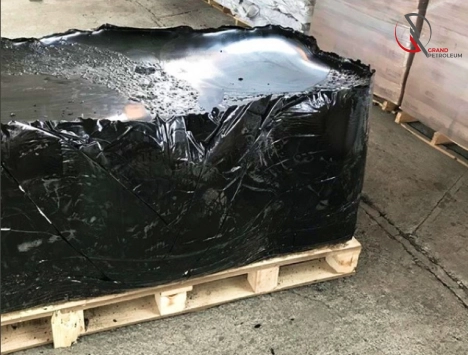
Catalytic Oxidation
In addition to the thermal cracking of bitumen, catalytic oxidation is even carried out to achieve oxidized bitumen. Hence, these catalysts are brought into action by being applied to the bitumen while heating/oxidating the bitumen. The heat with the inflow of air is responsible for the speeding up of the chemical reactions taking place in the chamber of the furnace with the use of air inflow. Thus, a low temperature and a shorter processing period are needed.
The catalytic process, which is prevalent in the modern age, yields some of the greatest benefits, which are better energy efficiency, reduced processing cost, and precise control of the product’s final characteristics. The first one poses new difficulties, for instance, the necessity to use catalysts and the question of the safety of using some catalysts.
Quality Control and Testing
Employing any processing technique but ensuring the quality of the product is guaranteed with stringent quality control measures is the secret to the unfailing operation of treated bitumen. Different tests and comparisons are done at different stages of the production process, as well as on the final product, for further verification of compliance with the standards set out and specifications.
Some of the key tests performed on oxidized bitumen include:
Penetration Test: This test gauges the degree of hardness or consistency of the asphalt by establishing the depth to which a pin loaded with a certain weight is inserted into the sample under specific conditions.
Softening Point Test: This test is called viscosity grade, and it shows the temperature at the transition of bitumen from a semisolid state to liquid, which indicates the temperature performance.
Ductility Test: This test determines the bitumen’s capacity to elongate and flow under deformation without cracking, which is the most vital for applications involving thermal expansion and contraction.
Aging Tests: Accelerated ageing testing mimics the long-time span effects of weathering and oxidation; thus, it is useful to predict the strength and service life of the material.
With the application of strict quality control processes and the achievement of standard set requirements, manufacturers have the assurance that oxidized bitumen products will perform well and will be reliable.
Advancements and Innovations
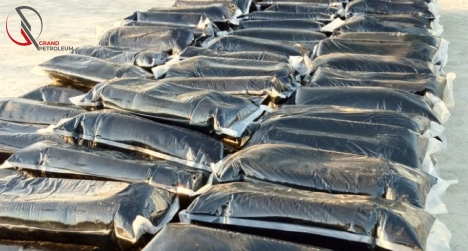
Like other materials, the environmental industry is innovating rapidly, and the success factors are often higher performance, sustainability and competitiveness. Here are some notable advancements and innovations in the field:
Nanotechnology Applications: Researchers are studying the chance of nano-silica, carbon nanotubes and nano clay application as the entities incorporated into the production of the oxidized bitumen. These nanomaterials can upgrade the mechanical properties as well as minimize challenges posed by wear and tear in extreme conditions. They are part of the high functionality of the material, which is reflected by its high durability.
Bio-based Oxidized Bitumen: The part of the plan which entails the substitution of fossil fuels by different sources is studying the potential of using biomass to derive alternate oxidized bitumen like used fatty acids and oils and some biomass oils. Fiber and lignin can be used as non-toxic and environmentally benign alternatives instead of oxidized bitumens that, under normal conditions, are in use.
Recycling and Reuse: Furthermore, the oxidized bitumen industry is one of the key agents of this solution, and therefore, the players are looking at recycling and reusing technologies to integrate oxidized bitumen back into the industry value cycle at the end of service life. That then could involve instead the development of the latest techniques and ways of ruthlessly separating and recovering those and then using the recycled stuff as feedstock for something else or diverting it into new materials.
Intelligent Monitoring Systems: Integration of sensors with a monitoring system to Smart Oxidized Bitumen Products application on a rooftop and road pavement structures can provide the users with product performance and condition reports over a specific period. This data is then utilized to predict repair schedules and smartly allocate resources, and thus, one can see the extension of the life of products.
Computational Modeling and Simulation: A novel multi-scale tier computational setting and new model simulations are also developed to make the process of oxidation of bitumen easy. They, in principle, allow the automation of production methods, the prediction of material behavior, and the creation of new formulas capable of satisfying requests for a particular purpose.
The innovations and developments that have been done can be utilized to improve the properties of materials, their service life, and sustainability during their use, keeping bitumen’s oxidation as one of the relevant technologies for numerous applications and economically feasible.
Installation and Application
Bitumen roofing membranes can be applied with a diversity of methods, such as torch application, hot mopping, or cold adhesives. The installation option selected takes into consideration factors like the room slope, the substrate type, and the project-specific needs, among others.
The process of installation also does not forget the importance of safety regulations, as expert roofing professionals follow the prescribed set rules and guidelines to ensure the safety of people and property and to comply with industry standards. Advocacy of proper ventilation, personal protective equipment (PPE), and compliance with local building laws and codes are the components of this mandate.
Maintenance and Repair
Just like any other roofing system, oxidized bitumen-based roofing membranes demand periodic maintenance and inspection in order to ensure their consistently good performance and define any possible problems and damages. Common maintenance tasks include:
• The inspector visually inspects cracks, blisters, or other telling signs of deterioration.
Removal of any trash or weeds that are growing is also part of the restoration process.
The usage of the compatible oxidized bitumen material is supposed to recover the local damages or defects.
Through regular inspections and maintenance practices recommended along with prompt action, the service life of the oxidized bitumen roofing systems can be increased and the roofing investment maximized.
The goal of this case study is to show the important position of oxidized bitumen in the roofing products market by creating resistant, weatherproof and durable roofing solutions for buildings and structures across the globe.
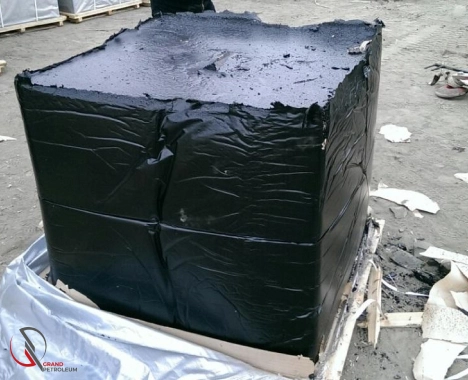
Oxidized Bitumen Business Review and Future Forecast
The global market for oxidized bitumen is projected to witness sustained growth in the upcoming years, which is being led by several factors, mainly the rising demand from construction and infrastructure sectors.
Roofing and Waterproofing: As the construction industry is rapidly expanding and there is an increasing necessity for roofing and waterproofing products that are long-lasting and high-performance, oxidized bitumen will be in great demand.
Road Construction and Maintenance: As the fuel that powers cars, the demand for oxidized bitumen in asphalt mixes for road pavement and maintenance will be on the rise.
Emerging Applications: Continuous research and development work is underway to find new applications for oxidized bitumen that are not limited to transportation infrastructures but include sound-dampening materials, coatings for renewable energy systems, and advanced construction materials.
Sustainability Efforts: As for the environmental concerns, makers are experimenting with more sustainable modes of production, such as the use of renewable materials and the adoption of energy-efficient processes.
Although the industry has the potential to expand, oxidized bitumen might be confronting issues of oil price fluctuations, changes in regulations and competition from alternative materials. Even though oxidized bitumen has inherent benefits and can be used in several industries, it still remains an essential material in various manufacturing sectors.
The conclusion is that oxidized bitumen is a multifaceted and efficient alternative to many others as it has a wide area of application in various sectors. Its particular features, including high-temperature resistance, weathering ageing resistance, flexibility, and durability, create the condition where it is an excellent option for critical use. The development and infrastructure sectors are set to be the major end-users of oxidized bitumen. Thus, the growing demand for the material will be accompanied by more inventions and innovations in the future.